In oil and gas drilling operations, the mud pump plays a pivotal role in circulating drilling fluid and maintaining downhole pressure. At the heart of this equipment lies the bearing, a small yet critical component that directly impacts drilling efficiency and operational safety. Once a mud pump bearing burnout occurs, it can trigger severe equipment downtime and even lead to system-wide failures. This article explores the main causes of mud pump bearing burnout and provides practical maintenance strategies to significantly extend bearing service life and reduce operational costs.
I. Top 3 Causes of Mud Pump Bearing Burnout
After evaluating multiple drilling team reports and field usage data, we’ve identified three main causes behind frequent mud pump bearing burnout:
1.Blocked or Leaking Oil Circuit
The oil circuit acts as the lifeline of the lubrication system. In harsh drilling environments, dust, mud, and other contaminants easily enter the system and gradually block the oil lines. Once lubrication is interrupted, bearings are exposed to dry friction, leading to overheating and eventual burnout.
Additionally, oil pumps like the CB50 gear pump require excellent sealing. If air enters the system, it reduces oil pressure, making it difficult to deliver lubrication to the bearings—another direct cause of mud pump bearing burnout.
2. Abnormal Oil Level
Oil level plays a decisive role in bearing performance:
- Too low: Bearings are under-lubricated, causing metal-to-metal contact, excessive friction, and heat buildup.
- Too high: Excessive oil stirring increases resistance and traps heat, leading to accelerated wear and eventual bearing burnout.
In both cases, improper oil levels can contribute to bearing failure and burnout.
3. Poor Bearing Quality
The material composition and manufacturing accuracy of the bearing determine its durability:
- Substandard alloy ratios, low hardness, or poor surface finishing can cause premature failure.
- Inferior bearings may appear fine visually, so choosing high-quality brands is crucial to avoid hidden risks.
🔗API Standards for Drilling Equipment – American Petroleum Institute
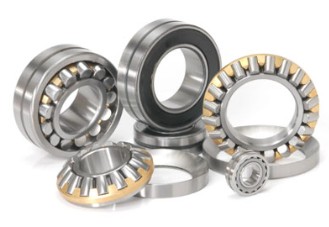
II. 5 Effective Methods to Extend Mud Pump Bearing Service Life
To prevent mud pump bearing burnout, apply these 5 field-tested strategies:
1. Regularly Clean and Inspect Oil Circuits
Routine maintenance of the lubrication lines is essential:
- Use compressed air to check for blockages in oil pipelines.
- Check seals and gaskets on oil pumps—especially CB50 gear oil pumps—to avoid air leaks.
- Replace aging seals promptly to ensure stable oil delivery.
2. Monitor and Maintain Proper Oil Levels
Daily inspections should include:
- Confirming the oil level is between the dipstick’s upper and lower limits.
- Inspecting the bearing housing for cracks or leaks.
- Calibrating dipsticks periodically to ensure accurate measurements.
3. Minimize Equipment Impact and Vibration
Excessive mechanical impact during transport or on-site movement can cause micro-damage:
- Secure the mud pump tightly during shipping.
- Avoid sudden starts or stops during operation to reduce shock loads on bearings.
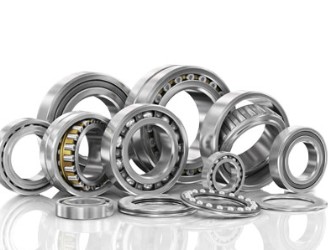
4. Maintain Lubricating Oil Cleanliness
Clean oil = long-lasting bearings:
- Use filtered, sealed containers to store lubricants.
- For forced lubrication systems (e.g., Baoshi, Qingzhou models), regularly filter or replace oil and perform monthly oil analysis.
- Splash lubrication models (e.g., Lanshi series) require planned usage due to complex maintenance procedures.
5. Choose Certified High-Quality Bearings
When selecting bearings:
- Inspect for visible surface defects and measure dimensional accuracy.
- Request inspection certificates and avoid unverified or “3-no” products (no brand, no date, no certification).
- Keep a bearing replacement log to monitor wear patterns and improve future procurement decisions.
Application Scenarios That Require Special Care
- Deep-Well Drilling: High-pressure, high-temperature environments demand heat-resistant, API-grade bearings.
- Offshore Platforms: High humidity and salt exposure make anti-corrosion coatings essential.
- Desert Drilling: Sand and dust contamination risks call for advanced sealing systems.
In all these scenarios, bearing burnout is more likely without vigilant oil system checks, proper sealing, and timely component replacement.

Conclusion: Better Maintenance for Better Performance
Mud pump bearing burnout is preventable with proper maintenance and quality control.
By focusing on lubrication management, oil level monitoring, and sourcing reliable components, drilling operations can extend bearing life, reduce downtime, and improve overall safety and efficiency.
Remember: Prevention is always better than repair. A small bearing failure can lead to major equipment downtime.
Need reliable mud pump bearings or maintenance support?
👉 Contact BESDRILL for OEM-quality mud pump spare parts and technical advice