Tapered roller bearings are critical components in industrial machinery, responsible for transmitting forces and enabling smooth motion. Their accuracy directly influences equipment stability, lifespan, and energy consumption. In high-precision fields such as automotive, rolling mills, metallurgy, and mining, even micrometer-level deviations can cause vibration, increased noise, and operational failures. This article provides a detailed overview of tapered roller bearing accuracy definitions, precision grade standards, and the eight key factors affecting bearing accuracy, offering valuable insights for bearing selection, usage, and maintenance.

Core Definitions of Precision in Tapered Roller Bearings
Precision in tapered roller bearings primarily involves two dimensions, both crucial for performance:
1. Dimensional Accuracy: Foundation for Proper Fit
Dimensional accuracy refers to critical size tolerances ensuring proper fit between the bearing and the shaft or housing, including:
- Bore diameter of the inner ring and outer diameter of the outer ring;
- Width tolerances of inner and outer rings;
- Diameter consistency and length tolerances of rolling elements (rollers).
Incorrect dimensional accuracy can lead to loose fits causing slippage or overly tight fits causing excessive friction and heat, both reducing bearing accuracy and service life.
2. Running Accuracy: Key to Smooth Operation
Running accuracy measures the bearing’s tolerance to wobble or runout during rotation and includes:
- Radial runout: lateral deviation of inner or outer ring relative to the rotation axis;
- Axial runout: end-face deviation along the axis;
- Tilt or angular misalignment between inner and outer rings;
- Perpendicularity of end faces to radial surfaces.
Poor running accuracy causes centrifugal force fluctuations, vibrations, and noise, which can trigger cascading failures — for example, rolling mill vibrations lowering product quality.
Precision Grades According to GB307 Standard
China’s GB307 standard classifies bearing precision from ordinary to high precision as: 0 → 6 → 5 → 4 → 2 grades, with increasing precision.
- Grade 0: General machinery (e.g., agricultural equipment, general motors);
- Grades 6 & 5: Precision machinery (e.g., machine tool spindles, automotive transmissions);
- Grades 4 & 2: High precision (e.g., high-speed rolling mills, precision boring machines).
Higher grades feature tighter dimensional and runout tolerances — for example, grade 2 bearings maintain radial runout under 5 μm, while grade 0 may allow 15-20 μm.
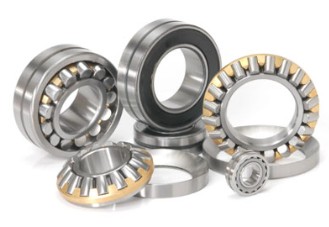
Eight Key Factors Influencing Running Accuracy of Tapered Roller Bearings
Multiple stages — manufacturing, assembly, inspection — affect the rotational accuracy of medium and large precision tapered roller bearings. The main factors include:
1. Variation in Roller Taper Angle
The taper angle of rollers ensures line contact with inner and outer raceways. Deviations cause uneven contact and stress concentration:
- Excessive angle: tight contact at large end with outer race, loose at small end causing uneven load;
- Insufficient angle: high stress at small end accelerating wear and lowering accuracy.
Roller angle consistency within 30 arcseconds is essential to avoid periodic vibration.
2. Roller Sliding Line Straightness
The roller’s sliding line (generatrix) must be straight. Curvature leads to point contact rather than uniform line contact, causing stress fluctuations and high-frequency vibration, especially at high speeds. Precision grinding achieves straightness within 2-3 μm/m.
3. Radial Movement of the Cage
The cage keeps rollers evenly spaced and guided. Excess radial clearance or deformation causes uneven roller distribution (“clustering”), increased friction, irregular vibration, and reduced synchronization. For grade 4 bearings, radial cage clearance should be ≤ 0.01 mm.
4. Perpendicularity of Cage Window Sliding Line
Deviation from perpendicularity between cage window (roller pockets) sliding line and cage face causes roller tilt and misalignment, leading to axial runout and fluctuating axial forces. Tolerance should be under 0.01 mm per 100 mm.
5. Roundness Error of Ring Raceway
Inner and outer raceway roundness directly affects radial runout. Errors include:
- Ovality: elliptical cross-section causing periodic radius changes;
- Polygonal shape: multiple corners causing vibration.
High precision raceways control roundness error within 3-5 μm; grade 2 requires ≤ 2 μm.
6. Straightness of Raceway Sliding Line
Deviation causes uneven roller-raceway contact, leading to stress concentration at roller center or ends, amplifying runout due to combined roller and raceway errors.
7. Assembly Process Quality
Even with precise parts, poor assembly reduces overall accuracy:
- Uneven roller placement or cage deformation;
- Misalignment between inner and outer rings increasing eccentricity;
- Incorrect preload causing excessive play or friction.
Automated assembly with precision tools can limit concentricity loss to under 2 μm.
8. Accuracy of Inspection Methods
Measurement errors arise if inspection instruments have insufficient precision or if measurement references are incorrect:
- Using lower grade instruments than bearing tolerance;
- Selecting non-ideal reference surfaces;
- Measuring outside stable temperature conditions (±2°C recommended) due to thermal expansion.
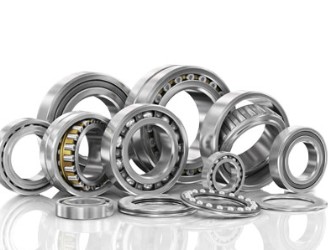
Risks of Inadequate Bearing Accuracy
Low bearing accuracy negatively impacts equipment through:
- Increased vibration and noise affecting user experience;
- Accelerated wear shortening bearing life by over 50%;
- Increased power consumption by 10-15% in high-speed applications;
- Safety risks in heavy machinery causing seizure or catastrophic failure.
Strategies to Improve Tapered Roller Bearing Accuracy
To enhance bearing precision:
- Use high purity bearing steel (e.g., SUJ2) with controlled heat treatment;
- Apply ultra-precision grinding for rollers and raceways;
- Employ robotic or precision tooling for assembly;
- Use higher precision inspection instruments in controlled environments;
- Select precision grade based on application, balancing cost and performance.
Conclusion: Accuracy Is the Lifeline of Tapered Roller Bearings
Bearing accuracy results from comprehensive control of design, materials, manufacturing, assembly, and inspection. Core factors include roller taper angle, raceway roundness, assembly concentricity, and measurement precision. Selecting suitable precision grades (GB307 grades 5 or 2) and maintaining installation and monitoring ensure long-term performance. For demanding applications like machine tools and high-speed trains, prioritizing certified high-precision bearings and reliable manufacturers is vital. Only by managing every detail from the source can tapered roller bearings truly deliver precise, reliable transmission.