Why Fishing Tools Are Essential in Drilling Operations
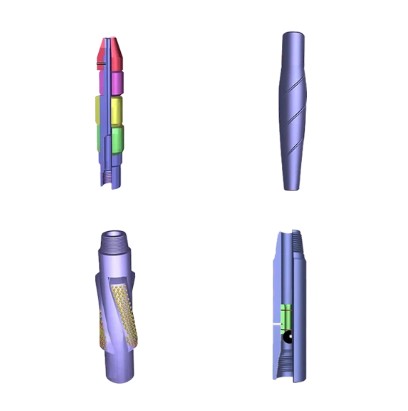
In modern oil, gas, and geothermal drilling, the occurrence of downhole stuck pipe, tool failure, or equipment loss—collectively referred to as “fish”—is a common and costly challenge. These fishing incidents cause significant Non-Productive Time (NPT), extending project durations and inflating operational costs.
Fishing tools play a vital role in safely and efficiently retrieving these fish to resume drilling operations promptly. BESDRILL fishing tools, integrating advanced mechanical engineering and material science, provide a comprehensive range of solutions tailored for complex downhole conditions, reducing downtime and enhancing drilling safety
1. Scientific Design Principles and Engineering Technologies Behind BESDRILL Fishing Tools
1.1 Mechanical Locking and Engagement Mechanisms: The Synergy of Mechanics and Structure
The fundamental purpose of fishing tools is to achieve reliable mechanical grip on downhole fish. BESDRILL fishing tools employ three primary engagement mechanisms:
- External Overshot Engagement
Utilizing multi-jaw overshot structures that encircle the fish’s external diameter. A slip ring mechanism combines taper and friction locking, suitable for cylindrical, intact drill pipe or casing. This design ensures uniform force distribution, minimizing tool wear and wellbore damage. - Internal Spear Engagement
Designed with a central mandrel that actuates expanding slips to grip the inner wall of the fish. Ideal for hollow or tubular fish such as casing sections. The slip material balances elasticity and strength to prevent deformation or jamming. - Threaded Tapered Engagement
Involves a precision-engineered tapered reverse thread that mates with corresponding threads inside the fish. This mechanical self-locking method is highly secure for threaded fish like stuck collars or tool components. Manufacturing tolerances are tightly controlled within microns to guarantee engagement integrity.
Additionally, high-strength permanent magnets are employed for non-mechanical magnetic fishing tools to recover small metallic debris, reducing interference with downhole structures.
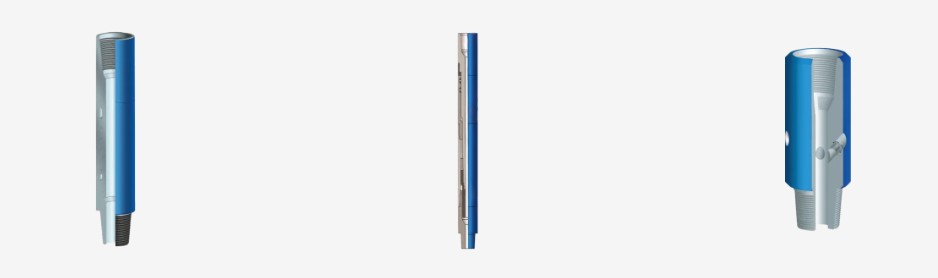
1.2 Materials Science and Surface Engineering: Ensuring Durability and Reliability
Given the harsh downhole environments involving high temperature, pressure, and corrosive fluids, BESDRILL optimizes material selection and surface treatments to ensure tool longevity:
- High-Strength Alloy Steel
Using 42CrMo and 35CrMo alloys, which offer excellent tensile strength, impact toughness, and fatigue resistance, enabling tools to withstand repeated heavy loads and impacts. - Surface Hardening Processes
Carburizing and nitriding treatments increase surface hardness to HRC58+, significantly enhancing wear resistance against abrasive drilling cuttings and mechanical friction. - Stress-Relief Heat Treatment
Precision heat treatment reduces residual manufacturing stresses, mitigating crack initiation and propagation during service. - Anti-Corrosion Coatings
Special coatings protect against corrosion from H₂S, CO₂, and other acidic downhole fluids, maintaining mechanical integrity over long-term use.
1.3 Precision Manufacturing and Modular Design: Boosting Efficiency and Serviceability
- Precision CNC machining controls critical dimensions to within 0.01 mm, ensuring high locking efficiency.
- Modular designs facilitate onsite part replacement, reducing downtime and maintenance costs.
- Anti-jamming and deblocking features minimize the risk of tool sticking during fishing operations in high-viscosity muds or complex formations.
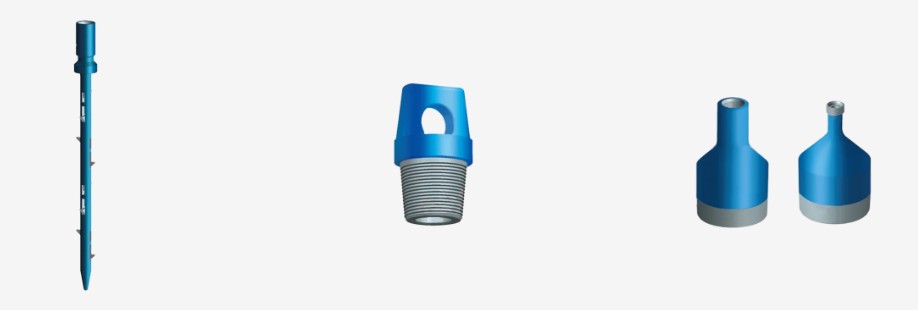
2. Detailed Overview of 7 Core BESDRILL Fishing Tool Types and Applications
2.1 Overshot Fishing Tool
- Features: Multi-jaw slip ring design envelops fish’s outer diameter and locks with taper friction. Compact and lightweight.
- Applications: Commonly used for retrieving broken drill pipes, casings with smooth outer surfaces.
- Operational Tips: Select proper slip material; routinely inspect slip wear to avoid disengagement.
2.2 Internal Fishing Spear
- Features: Central mandrel forces slip arms outward to grip internal bore of tubular fish. Made of high-elasticity alloy steel.
- Applications: Hollow fish such as casing fragments, larger diameter tubular fish.
- Operational Tips: Ensure spear is centered during insertion to avoid uneven slip load and jamming.
2.3 Tapered Thread Fishing Tool
- Features: Precisely machined reverse tapered threads mechanically lock with fish’s internal threads.
- Applications: Threaded fish like stuck collars and downhole tools.
- Operational Tips: Maintain thread cleanliness to ensure full engagement.
2.4 Magnetic Fishing Tool
- Features: High-strength neodymium magnets attract and hold ferrous metal debris non-mechanically.
- Applications: Retrieval of small magnetic metal fragments with minimal risk of tool sticking.
- Operational Tips: Confirm debris magnetism; optimize magnet size and placement.
2.5 Reverse Circulation Junk Basket
- Features: Utilizes drilling fluid reverse circulation to trap debris at well bottom.
- Applications: Removing debris accumulation to prevent future tool sticking.
- Operational Tips: Control reverse circulation pressure to avoid deformation.
2.6 Fishing Jar
- Features: Hydraulic or spring-driven mechanism generates longitudinal impact forces to free stuck tools.
- Applications: Often paired with fishing tools to release stuck pipe and fish.
- Operational Tips: Adjust impact energy to prevent excessive tool or wellbore damage.
2.7 Mill Shoe
- Features: Equipped with tungsten carbide teeth for rotary grinding of stuck fish.
- Applications: Assists in mechanical retrieval of difficult fish by grinding.
- Operational Tips: Maintain optimal rotational speed to prevent overheating.
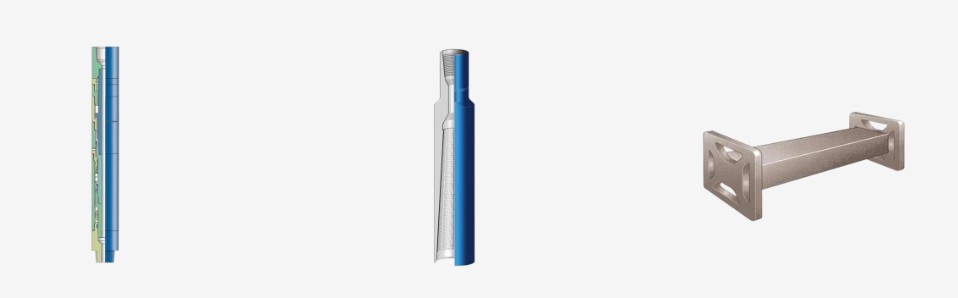
3. BESDRILL Fishing Tools Operation Protocols and Safety Guidelines
3.1 Precise Tool Selection for Optimal Recovery Success
- Employ logging, downhole cameras, and wellbore instrumentation to acquire detailed fish profile and dimensions.
- Match fishing tool model to wellbore size, fish diameter, and downhole conditions.
- Design combination fishing assemblies for complex fish shapes ensuring comprehensive engagement.
3.2 Standardized Procedures to Ensure Safe Operations
- Deploy tools slowly and accurately to avoid wellbore damage or fish displacement.
- Maintain mud circulation to minimize tool sticking and wear.
- Monitor hook load and torque in real-time to prevent overload.
- Use fishing jars judiciously to release stuck fish.
3.3 Regular Maintenance to Prolong Tool Life
- Inspect springs and slips for fatigue and wear; replace as necessary.
- Conduct periodic heat treatment checks to verify material integrity.
- Maintain detailed usage and maintenance logs.
3.4 Adherence to Industry Standards to Protect Personnel and Equipment
- Follow API RP 54 drilling safety guidelines strictly.
- Comply with NACE corrosion-resistant materials standards.
- Provide continuous staff training on technical and safety practices.
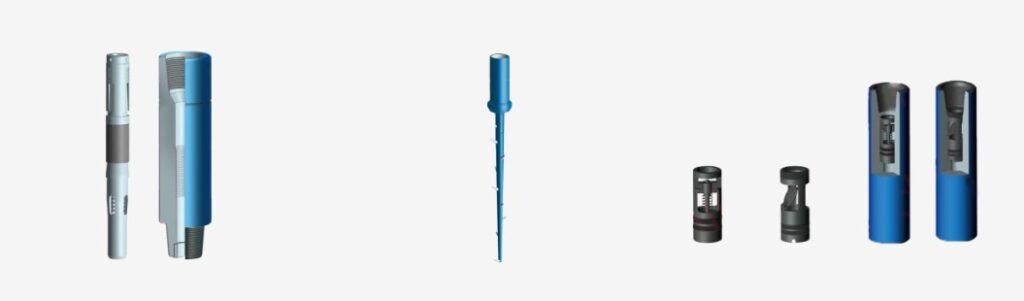
4. Conclusion
Downhole fishing remains one of the most technically demanding aspects of drilling operations. BESDRILL fishing tools leverage cutting-edge mechanical design and materials technology combined with precise operational protocols to deliver reliable, efficient fish recovery solutions.
Choosing BESDRILL means entrusting your operations to proven quality and professional expertise, minimizing downtime, and maximizing drilling performance. Contact BESDRILL today for tailored fishing tool solutions to meet your project’s unique demands.
BESDRILL fishing tools utilize advanced mechanical design and material science to ensure efficient and safe downhole fishing operations. For detailed specifications, please visit our product page 🔧.
Understanding and adhering to industry standards is crucial. Please refer to the API RP 54 safety guidelines 📜 to ensure personnel and equipment safety during operations ⚠️.