1. Industry Demands and Positioning of the W446 Mud Pump
The W446 mud pump by BESDRILL is engineered to meet the demanding needs of modern drilling operations. This W446 mud pump delivers precise pressure control, high flow efficiency, and long-lasting durability under extreme conditions. Whether applied in shale gas extraction, geothermal drilling, or deep well operations, the W446 mud pump performs consistently with reduced downtime and improved productivity.
With a cast-steel frame, modular piston systems, and compatibility with electrical or diesel drive, the BESDRILL W446 mud pump adapts easily to a wide range of drilling scenarios. Its compact structure and simple maintenance design make it ideal for onshore and offshore drilling applications.
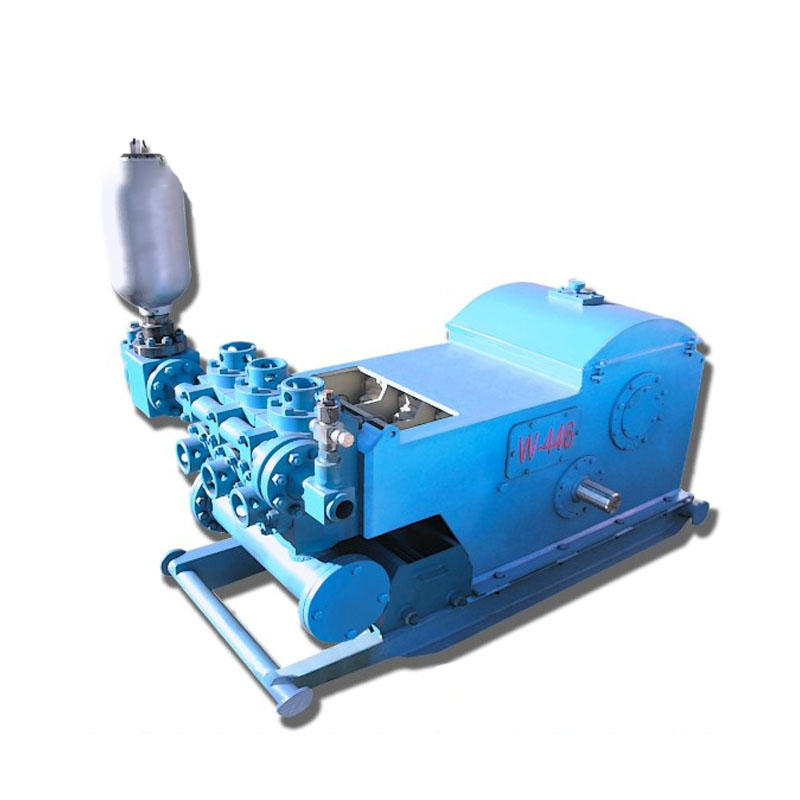
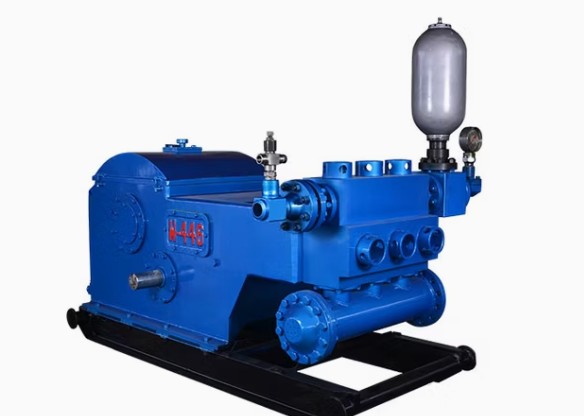
2. Technical Architecture of the W446 Mud Pump
(a) Fluid Dynamics System Design
1.High-Pressure Flow Control of W446 Mud Pump
The W446 mud pump employs a multi-stage plunger-sleeve coordination system with optimized plunger motion following a sinusoidal acceleration curve. This ensures precise matching between stroke frequency (50-300 strokes/min) and flow output. For example, with a 6-inch sleeve, at 300 strokes/min, it delivers 2502 L/min. Coupled with CFD-optimized flow channels, it minimizes turbulence losses. At 328 kW input power, pressure conversion efficiency exceeds 85%, guaranteeing stable high-pressure delivery (e.g., 1027 PSI at 6-inch sleeve), meeting ultra-deep well lifting requirements.
2.Smart Pressure Compensation System
Equipped with pressure sensors and variable-frequency closed-loop control, it continuously monitors discharge pressure fluctuations. When drilling fluid viscosity or annulus resistance changes, the system automatically adjusts stroke frequency and pump speed, maintaining pressure deviation within ±3%, preventing risks like kicks or blowouts. This meets the precise pressure control demands of shale gas horizontal wells, deepwater, and high-temperature/high-pressure wells.
(b) Durability Design of the W446 Mud Pump
1. Wear-Resistant and Corrosion-Resistant Components
Pump sleeves use bi-metal composite plating (high-chrome cast iron inner layer + tungsten carbide outer layer), with surface hardness HRC 65-70, offering three times the wear resistance of traditional sleeves. Plunger seals use graphene-enhanced fluororubber, rated for 180°C and 20,000 PSI, extending seal life beyond 200 hours and resisting corrosion from H₂S, CO₂, and other harsh environments, suitable for acidic gas fields.
2. Reinforced Power End Design
The crankshaft is made by integral forged milling, with nitrided and polished journals, improving fatigue strength by 40%. Connecting rods feature self-aligning sliding bearings with forced lubrication (independent gear pump and oil pressure monitoring), achieving “zero clearance” adaptive compensation. Under continuous 1200 rpm operation, vibration stays below 2.5 mm/s, ensuring long-term reliability.
3.Technical Specifications of W446 Mud Pump
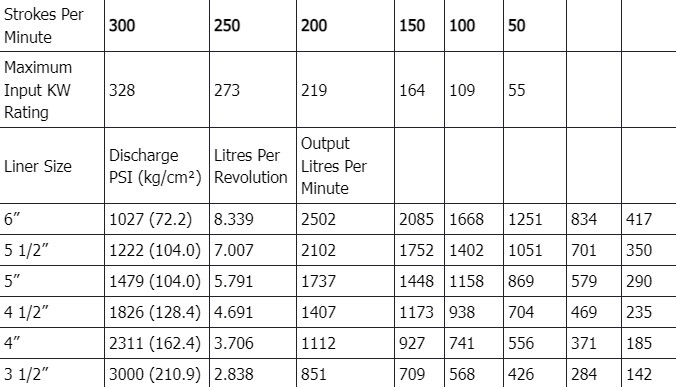
4. Multi-Scenario Application Advantages
Oil & Gas Exploration
The W446 supports switching between high-pressure low-flow precise cuttings transport and high-flow pulsating rock breaking modes. With a 4-inch sleeve at 250 strokes/min, it outputs 1407 L/min at 1826 PSI for efficient cuttings transport. Switching to a 6-inch sleeve at 100 strokes/min delivers 834 L/min at 1027 PSI, assisting pulsating jet technology to break hard formations and boosting mechanical drilling rates by 20-30%, ideal for complex formations like Longmaxi and Fuling shale gas.
Water Well and Geothermal Development
Thanks to its wide power range and low-energy design, at 50 strokes/min it consumes only 55 kW, delivering 142 L/min with a 3.5-inch sleeve, meeting typical water well circulation needs. At 200 strokes/min with a 5-inch sleeve, it outputs 1158 L/min at 1479 PSI, efficiently penetrating geothermal reservoir fractures. In North China Plain geothermal projects, it reduces single-pump operational costs by 15%.
Overseas Market Breakthrough
Certified to API 7K, the W446’s intelligent control system seamlessly integrates with digital oilfield platforms like Schlumberger DrillPlan for remote pressure and flow control. Equipped with desert protection kits (forced air radiator cooling and dust filtration), it operates reliably in 50°C desert environments. It has earned procurement approvals from major oil companies such as Saudi Aramco and ADNOC.
“According to API Specification 7K requirements, the W446 mud pump is fully certified.”
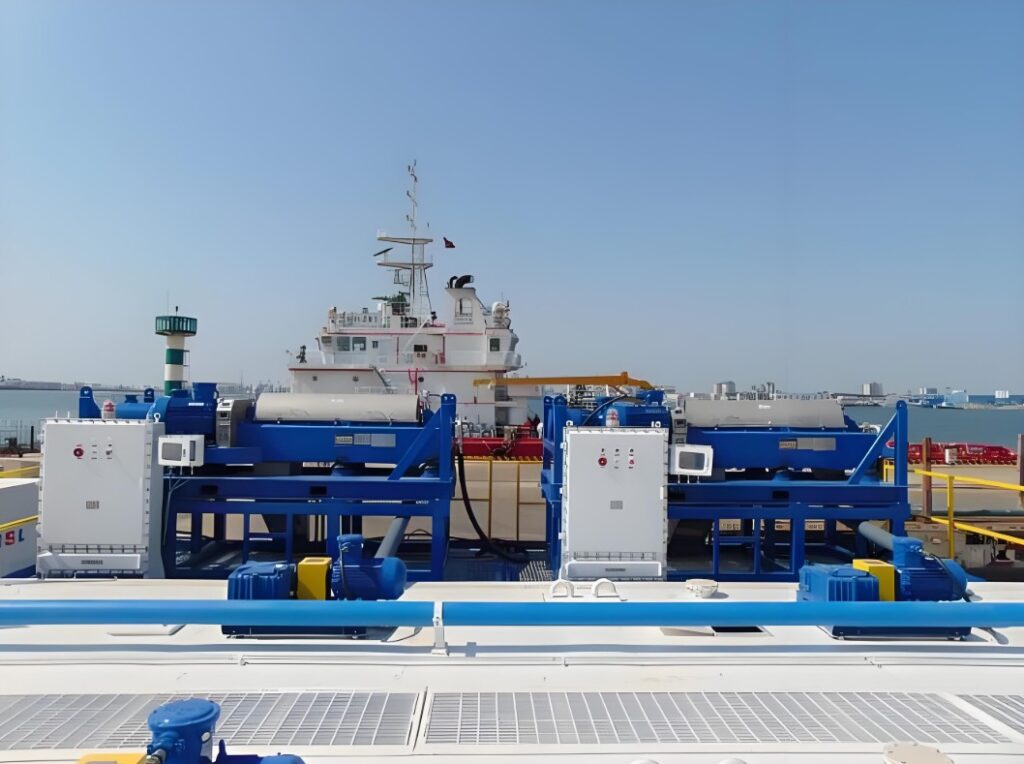
5. Total Cost of Ownership (TCO) Optimization
Preventive Maintenance System
Supports intelligent operation & maintenance management via vibration and temperature sensors collecting pump data in real-time. Using digital twin technology, it predicts wear trends and provides 72-hour advance warnings for replacing wear parts (sleeves, seals). Standardized maintenance kits enable “1-hour quick replacement,” reducing annual maintenance costs by 25%.
Energy Saving and Efficiency
Employs permanent magnet synchronous motors with variable frequency drives, saving 15-20% energy compared to traditional asynchronous motors. Optimized pump efficiency (volumetric ≥95%, hydraulic ≥88%) saves over 100,000 RMB in electricity costs during a 1,000-hour operational cycle, supporting green drilling under carbon neutrality goals.
Conclusion
Driven by technological breakthroughs for performance upgrades and scenario adaptability to reshape operational modes, the Besdrill W446 mud pump leads the industry in high-pressure performance, durability, and intelligent control. From complex oil and gas fields to green drilling initiatives, W446 is not just equipment but a technology engine for efficient, reliable, and low-carbon drilling—powering global energy development with “Made in China” innovation and advancing mud pump technology from follower to leader.
You can visit our Product Center page for detailed information.