Handling refers to the ways in which products, materials, or goods are managed, transported, and stored throughout the supply chain. Effective handling is crucial to ensure that products are delivered on time, in good condition, and at optimal cost. Whether you’re managing inventory in a warehouse, shipping products to customers, or moving materials between production stages, the right handling methods can streamline operations, reduce damage, and enhance customer satisfaction.
- Manual Handling
Manual handling refers to the use of human labor to move, lift, carry, or place products. This type of handling is commonly used for smaller, lighter goods or in environments where automation isn’t feasible. It is a direct and cost-effective way of handling products in situations where the use of machines is not practical.
However, manual handling comes with certain risks. Workers involved in this type of handling are more prone to injuries such as strains, sprains, and musculoskeletal disorders. As such, it’s important for businesses to implement safety protocols and provide training on proper lifting techniques. While manual handling might be suitable for small operations, as the volume of goods increases, companies may find it beneficial to invest in automated solutions.
Benefits of Manual Handling:
Cost-effective for small-scale operations.
Flexible and adaptable to various tasks.
No initial capital investment for machinery.
Mechanical handling refers to the use of equipment such as forklifts, conveyors, cranes, and pallet jacks to transport materials. This method is particularly useful for heavy or bulky items that are difficult or unsafe to handle manually. Mechanical handling significantly improves speed, efficiency, and safety in material transport.
A key advantage of mechanical handling is its scalability. As businesses grow and the volume of materials increases, mechanical handling can accommodate this growth without a proportional increase in labor costs. Furthermore, it reduces the physical strain on workers and minimizes the risk of injury. Modern mechanical handling systems often incorporate automation, reducing the need for human intervention even further.
Benefits of Mechanical Handling:
Suitable for heavy or large products.
Enhances speed and efficiency.
Reduces labor costs and injury risks.
- Automated Handling
Automation is increasingly becoming a cornerstone of modern material handling. Automated handling systems use advanced technologies such as robotics, automated guided vehicles (AGVs), and warehouse management software to move and organize materials without human intervention. Automated systems are designed for high-volume, repetitive tasks, making them ideal for industries like manufacturing, logistics, and e-commerce.
Automated handling offers exceptional speed, accuracy, and reliability, allowing businesses to meet high customer demands without sacrificing quality. Automation also eliminates the variability associated with human labor, ensuring consistency and reducing the risk of errors. Although the initial investment in automated systems can be high, the long-term savings in labor costs and improved operational efficiency make it a worthwhile investment for many businesses.
Benefits of Automated Handling:
High speed and precision in material handling.
Reduces human error and labor costs.
Optimizes warehouse space and productivity.
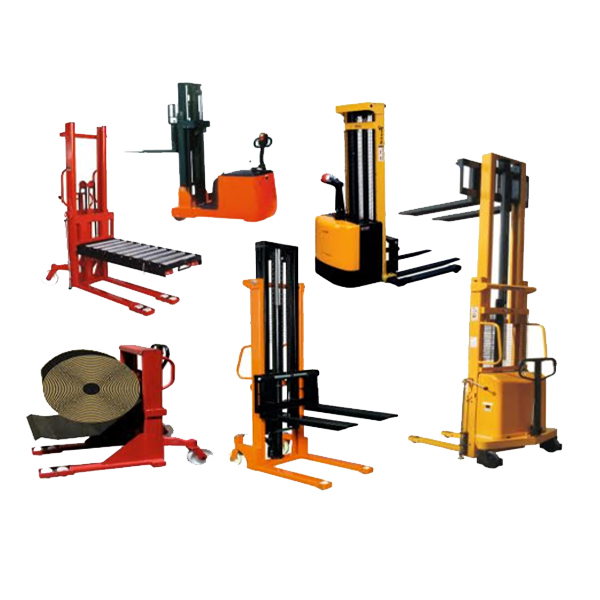
- Storage Handling
Storage handling focuses on the methods used to store materials in a way that maximizes space and minimizes access time. Efficient storage handling can significantly reduce costs associated with warehousing and inventory management. Methods like pallet racking, shelving, and bin storage are common in both large and small operations.
Warehouse management systems (WMS) can be integrated with storage handling systems to optimize space utilization and streamline order fulfillment. For example, automated storage and retrieval systems (AS/RS) are used in large warehouses to quickly locate and retrieve products, reducing the need for manual searching and improving overall efficiency.
Benefits of Storage Handling:
Optimizes space utilization in warehouses.
Improves access and retrieval times.
Reduces labor costs associated with searching for items.
Benefits of Packaging Handling:
Protects products from damage during transit.
Facilitates easier and safer transportation.
Enhances the overall customer experience with well-presented products.
- Shipping and Distribution Handling
Shipping and distribution handling is the final stage in the supply chain, where goods are prepared for delivery to customers. This type of handling involves organizing products for shipment, managing transport logistics, and ensuring that goods reach their destination in good condition and on time.
Choosing the Right Handling Solution for Your Business
Selecting the most appropriate type of handling depends on various factors, including the size of your business, the nature of your products, and your budget. Smaller businesses with limited budgets may rely more on manual or mechanical handling, while larger operations with high volumes of goods might benefit from automated solutions.
Investing in the right handling systems can lead to significant improvements in productivity, cost savings, and customer satisfaction. By understanding the different types of handling available, businesses can make informed decisions to optimize their supply chain and stay competitive in their respective markets.
As technology continues to evolve, new handling methods and tools will likely emerge, offering even more opportunities for efficiency and growth. The key is to stay informed and adaptable, ensuring that your handling methods align with the demands of your business and your customers.