Blowout Preventer (BOP) A blowout preventer (BOP) is a large, specially designed valve device or mechanical system designed for tight containment, precise control, and real-time monitoring of oil and gas Wells to effectively prevent blowout accidents. A blowout is a sudden, high-speed ejection of crude oil, natural gas, or other fluid from a drilling hole without proper control. These blowout preventers are typically deployed at the wellhead and integrated with a range of other valves and safety equipment to form a reliable barrier that ensures safe drilling operations.
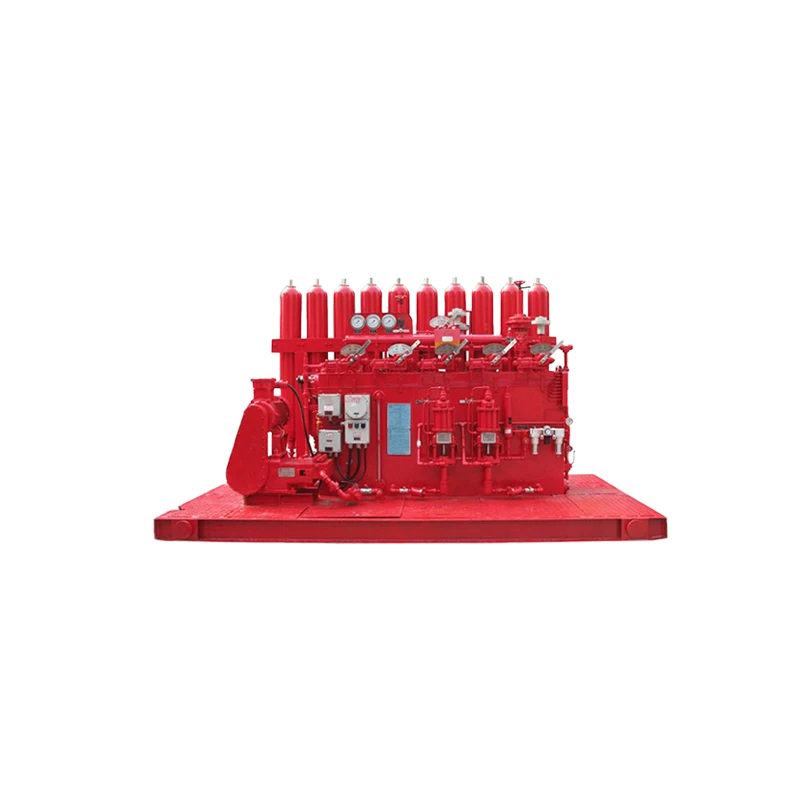
These equipment components must:
close the top of the hole
control the release of fluids
permit pumping into the hole
allow movement of the inner string of pipe
be activated independently.1
A BOP (Blowout Preventer) assembly is a complex and sophisticated system, usually made up of several key components:
Annular BOP (also known as “spherical BOP”)
This is a device that can form a seal around the drill pipe, suitable for a variety of diameters, and is the first line of defense against blowouts.
Rotary Ring BOP
Specifically designed for use in underbalanced drilling environments or where drilling operations need to continue while the BOP is closed. They allow the wellhead to rotate within a certain range while maintaining a seal, and can sometimes be used as a shunt.
Fixed hole ram
Designed specifically for different sizes of drill pipe in the drill string, it is solid and tightly wraps the drill pipe to ensure the tightness of the drill string under specific conditions.
Variable orifice gate
Adjustable to accommodate different pipe sizes, providing greater flexibility and adaptability.
Blind ram or fully closed ram (CSO)
Used to close and seal the wellhead when the drill pipe is withdrawn from the hole, preventing the outflow of fluid.
Blind shear ram
In case of emergency, it can cut the drill pipe in the well and quickly close the wellhead to achieve complete sealing. It is the key equipment to control the serious blowout accident.
The shear ram requires great force to cut through the drill pipe, especially the tool joint, and is an indispensable component of the subsea blowout preventer.
Drilling four (also known as “mud cross”)
Flange or wheel type components connecting the parts of the blowout preventer, the outlet connects the throttle manifold and the kill line, responsible for the circulation and control of drilling fluid.
Casing bowl
Part of the wellhead assembly that holds and seals the upper end of the casing string and provides access to the annular space.
Adapter four-way (DSA)
Used to connect casing bowls to other parts of the BOP assembly to ensure integrity and tightness of the system.
Shim four
Used to adjust the height of the BOP components on the derrick to ensure accurate alignment and sealing between components.
Mud riser/bell joint/flow joint
An important component that guides the circulation of drilling fluid, has an inner diameter equal to or greater than the BOP opening, has an outlet on the side to direct drilling fluid to the shaker or mud pit, and has an inlet to fill the line.
The configuration of the BOP unit can be flexibly adjusted according to the specific pressure rating, drilling conditions and safety requirements.
For example, some operations choose to install additional blind or CSO RAMS under the top pipe ram or annular BOP to enhance pipeline safety.
In addition, the rotary ring BOP is sometimes placed above the ring BOP to replace the mud riser to seal the wellhead during drilling, further improving safety and flexibility.
The identification of the BOP group is mainly achieved by its pressure rating, internal opening size, and the layout of the BOP and drilling four channels.