Handling equipment refers to a wide range of machinery, tools, and devices that assist in the movement, storage, control, and protection of materials and products. It is designed to make processes easier, faster, and more efficient while reducing the physical strain on workers. This equipment is used across different stages of production, logistics, and distribution, helping companies optimize their operations.
Whether it’s moving raw materials within a factory, transporting goods in a warehouse, or lifting heavy items, handling equipment plays a critical role. It encompasses everything from simple hand tools, like carts and trolleys, to complex automated systems, such as conveyor belts, forklifts, and cranes.
Types of Handling Equipment
Handling equipment can be categorized into four primary types, each serving a distinct function in material movement and storage:
Manual Handling Equipment
This category includes basic tools like hand trucks, pallet jacks, and dollies. These devices require human effort to operate and are best suited for moving smaller, lighter loads. Although simple, they are essential for short-distance transportation and loading tasks. Manual handling equipment is cost-effective and offers flexibility in smaller warehouses or facilities with limited space.
Automated Handling Systems
Automated handling systems are more advanced and involve minimal human intervention. Conveyor systems, automated guided vehicles (AGVs), and robotic arms are common examples. These systems are used in industries where speed, precision, and efficiency are crucial, such as automotive, electronics, and e-commerce sectors. Automation reduces the risk of human error and increases productivity by handling large volumes of materials quickly.
Storage and Retrieval Systems
Proper storage is crucial for maintaining organized workflows. This category includes equipment like racks, shelving, bins, and automated storage and retrieval systems (AS/RS). These systems ensure that materials are stored in an organized manner and can be easily accessed when needed. In large warehouses, AS/RS technology can automatically locate and retrieve items, further streamlining the process.
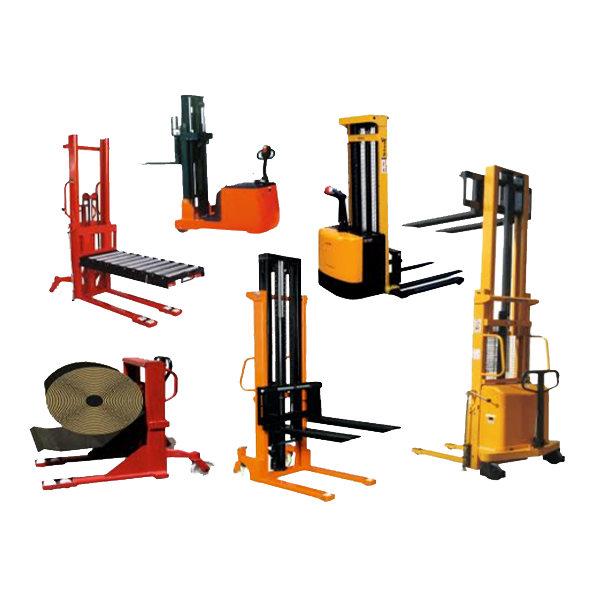
Industrial Trucks and Lifting Equipment
Forklifts, cranes, and hoists fall under this category. These machines are designed to lift, lower, and transport heavy loads that manual labor cannot handle. Forklifts are widely used in warehouses for moving pallets, while cranes are indispensable in construction and manufacturing industries for lifting heavy equipment and materials to great heights.
The Importance of Handling Equipment
Efficient material handling is the backbone of many industries. Poor handling processes can lead to damaged goods, wasted time, and increased labor costs, all of which negatively affect profitability. Here are a few reasons why handling equipment is vital for modern businesses:
- Increased Productivity
Handling equipment significantly enhances productivity by reducing the time and effort required to move materials. Automated systems, for example, can transport goods across a warehouse faster than any human worker, allowing companies to process orders quicker and meet customer demands more effectively. The faster a company can move materials, the more products it can manufacture or ship in a given period. - Improved Worker Safety
Manual handling of heavy loads poses a significant risk to worker safety, potentially leading to injuries and lost working hours. By using the right handling equipment, businesses can reduce these risks, creating a safer working environment. Lifting equipment like forklifts or cranes allows workers to handle heavy materials without the risk of physical strain, while automated systems remove the need for human involvement in potentially dangerous tasks.
- Cost Reduction
Though handling equipment may require a significant upfront investment, the long-term cost savings are considerable. Automation reduces the need for a large labor force, lowers the risk of product damage, and improves efficiency, all of which lead to lower operational costs. Additionally, proper material handling minimizes the risk of accidents and injuries, cutting down on insurance and compensation costs. - Better Space Utilization
In warehouses and manufacturing plants, space is often at a premium. Handling equipment, such as storage and retrieval systems, allows businesses to make better use of their available space. Vertical storage solutions and compact automated systems enable companies to store more products in a smaller area, increasing the facility’s overall capacity without the need for expansion. - Enhanced Product Quality
Handling equipment ensures that materials are moved and stored in a manner that minimizes damage. Automated systems, for example, handle products more gently than manual labor, reducing the chances of mishandling. By preventing product damage during handling, companies can maintain high-quality standards, reduce returns, and increase customer satisfaction.
Choosing the Right Handling Equipment
Selecting the right handling equipment depends on the specific needs of your business. Factors such as the size of your facility, the types of materials you handle, and your production volume all play a role in determining the most suitable equipment. Companies must assess their current workflows and identify bottlenecks where handling equipment can make the most significant impact.
Investing in handling equipment is a long-term decision, and it’s important to choose solutions that are both scalable and adaptable to future needs. Partnering with a trusted supplier can help you find the right equipment and provide ongoing support, ensuring that your material handling processes remain efficient as your business grows.
Handling equipment is an indispensable part of modern industry, driving efficiency, improving safety, and reducing costs. From simple manual tools to sophisticated automated systems, the right handling equipment can transform a business’s operations, allowing it to thrive in competitive markets.